KSK'S DNA:
KAIZEN
Employees capable of detecting waste (muda) and overstrain (muri) put their skills to use in Kaizen activities (CIP). This not only leads to products that customers are satisfied with; it also enables our staff to improve their 'human skills' and workplace competence on a daily basis.
Kaizen Concept
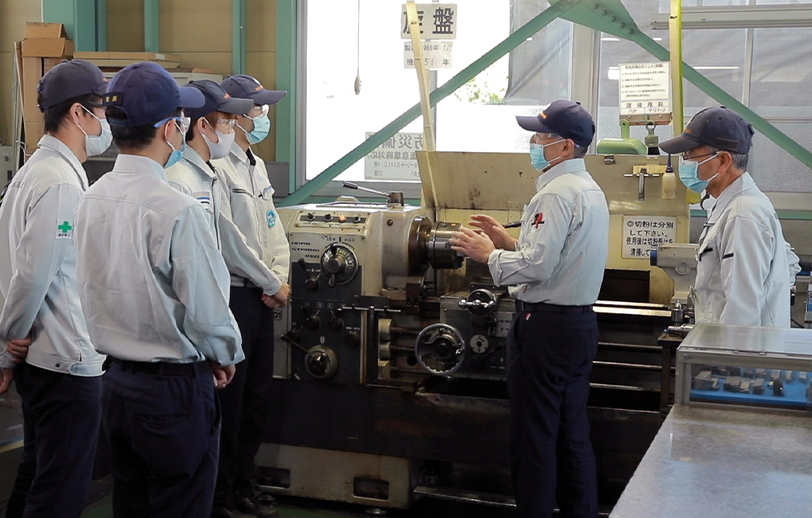
Bottom-Up and Top-Down
The Basis of Improvement Activities - Best When Combined
We have a bottom-up approach. Volunteers who wish to improve their skills are tasked with identifying impediments and waste in the workplace. They then come up with proposals and make improvements, thereby reducing working hours and cutting costs. On the other hand, we are also top-down oriented: Constantly challenging ourselves to ensure high quality, to create new technologies, and to carry out fundamental research through a variety of projects and collaborative efforts .
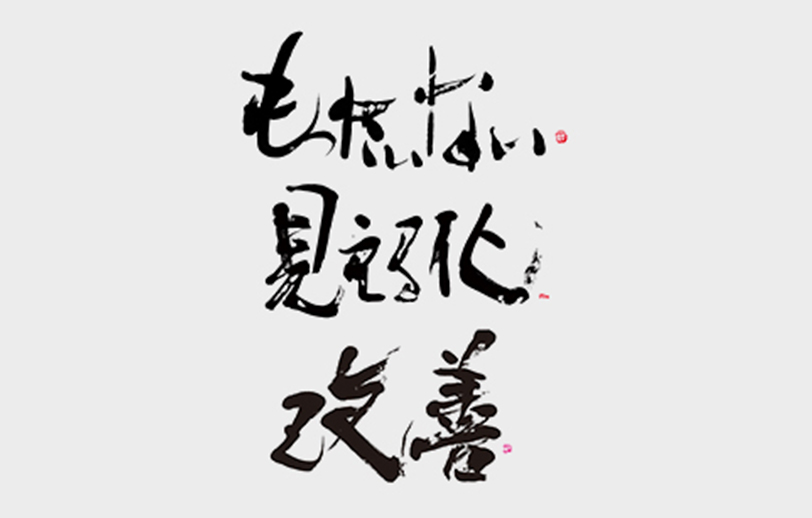
Action Pointers for Improvement Activities
'Too Good to Waste', 'Transparency', and 'Kaizen'
A guide for employees to promote improvement activities. The idea is to identify any waste and impediments in the workplace via the concept of 'Too Good to Waste'. In the 'Transparency' phase, the waste is visualized so that everyone can understand how it occurs. Finally, we analyse the root cause and transform this into 'Kaizen', i.e. making improvements.
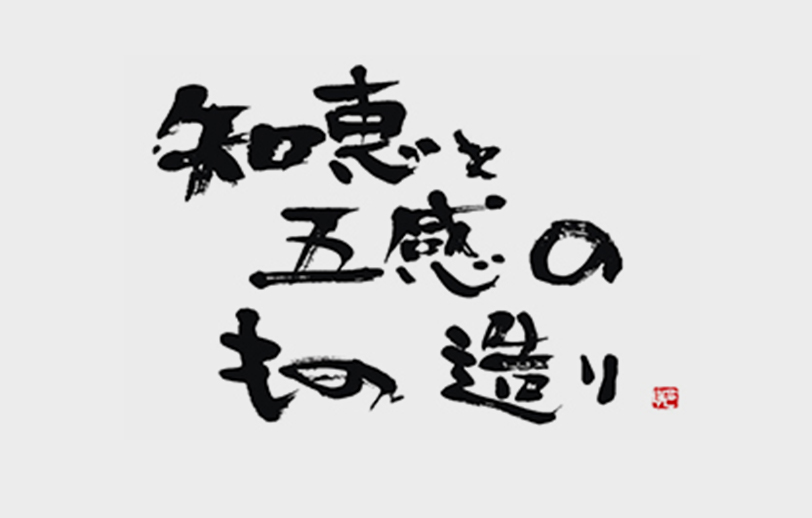
KSK Manufacturing Philosophy
The Fusion of Analogue and Digital
Even with the advent of digital technology, it is humans who build the systems, equipment and machines, and it is human intelligence that drives the improvements and reforms. In order to detect and solve machine anomalies and problems before they occur, the 'five senses' of sight, hearing, smell, taste and touch are required. This combination of intelligence and the five senses, bringing an analogue sensibility to the world of digital manufacturing, may be said to be the essence of KSK's manufacturing philosophy.
KSK Kaizen Convention
The Climax of the Year’s Kaizen Activities
Building People to Support Growth and Transformation
We hold our annual 'KSK Kaizen Convention' in July each year to confirm the results of the year's improvement activities and to act as a catalyst for Kaizen. Eight teams from the qualifying round from within the company, as well as invited teams from overseas, present their activities to the judging panel with the aim of winning the 'Grand Prize'.
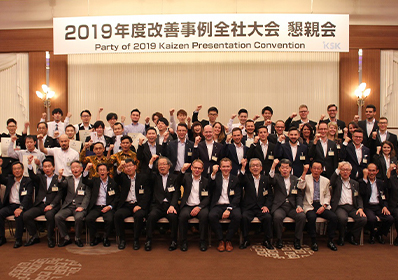
"Do our best!" from the Main Members
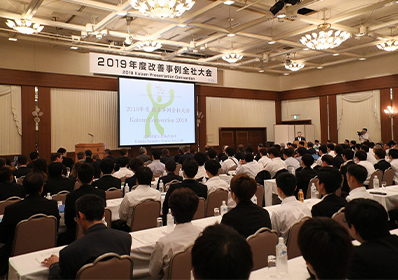
Scene inside the Convention
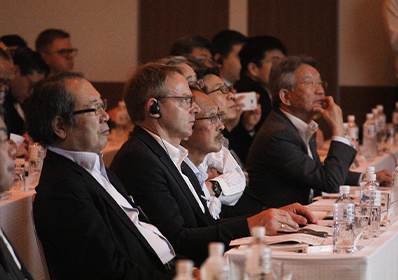
Serious Looks on the Judges’ Faces
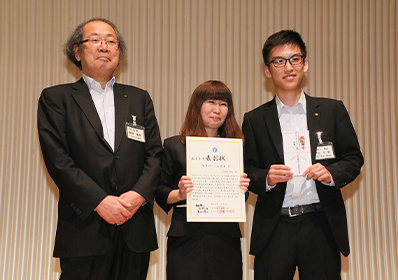
Announcement of the Winners
250
Attendants at the Kaizen Convention
31 Teams
Quality Circles Performing Daily Improvement Activities
Small Group (Quality Circle) Activities
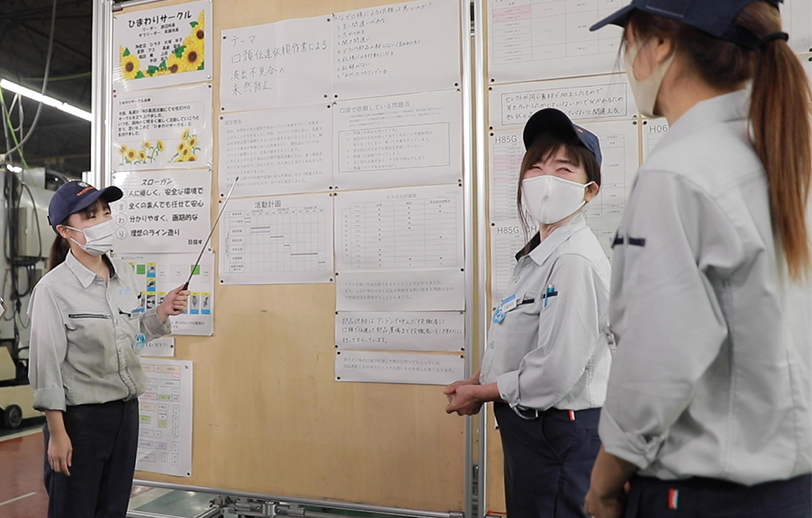
Basics of KSK Improvement Activities
Everything Starts with a Problem Affecting the Team
Our workforce is divided into 31 small teams. They take on the impediments and waste in the workplace, come up with proposals and make improvements, thereby reducing working hours and cutting costs. This is what we are aiming for: members train the basics of improvement in small groups, while at the same time their Quality Circle activities increase productivity and stimulate communication in the workplace.
Further Activation Plan
Volunteers with a Common Vector
'Creativity & Ingenuity Kaizen System'
In order to further revitalise the company, we have moved to "improvement team activities with like-minded people who can think for themselves".
Rather than waiting for instructions, such people can identify problems and make improvements on their own, taking responsibility and pride in making these improvements. The aim is to develop the potential of our staff and to combine that in teams.
In addition, we will further accelerate the improvement process by upgrading the existing suggestion system to a 'Creativity & Ingenuity Kaizen System' in which employees can evaluate and implement their own improvement proposals.
Training
Our Place of Learning: Skills Dojo
Transferring Skills and Building People
No matter how digitalised the world is, it is human skills, intelligence and senses that operate machines and determine quality, and it is humans who stimulate improvements.
At the Skills Dojo, we work as a team, developing human competence and shopfloor expertise in order to further strengthen our company’s Kaizen and manufacturing skills.
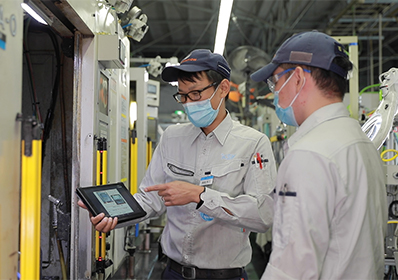
Training Scenes: Practical Training
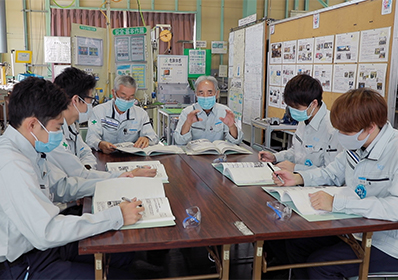
Training Scenes: Lecture
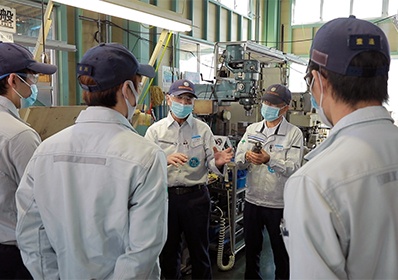
Training Scenes: Practical Training
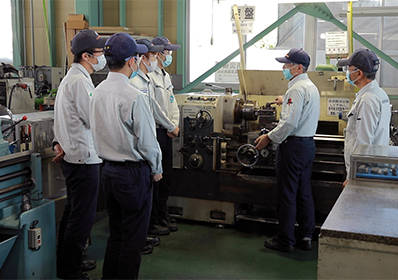
Training Scenes: Practical Training